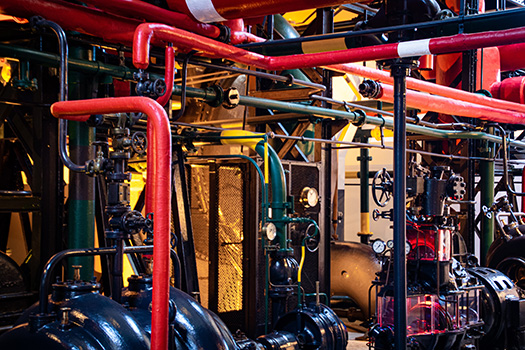
Introduction
Fuel cleanliness plays a vital role especially in the industries where the fuel is used as lubrication for heavy machinery and as an industrial product for commercial purposes. Clean fuel could appear contaminated or a heavily contaminated sample can appear very clean when the steps are not astutely taken. Particle counting techniques are employed to monitor fuel cleanliness to ensure product quality and longevity of equipment for hydraulics applications.
Fuel Analysis – Particle Counting Method
Particle counting is the process of detecting and measuring the size and quantity of particles (contaminants) distributed in a fuel/suspension. There are a variety of instruments commercially available to optically count particles; from portable units for onsite, to large, sophisticated lab-based instruments.
The common technique used by these instruments is either a white light source or a laser beam. This works by passing the sample liquid suspension between a light source and a detector.
In the typical Beckman Coulter liquid particle counter (HIAC PODS), the light source is a laser diode, which illuminates individual particles in the sample to generate a shadow or blockage of light on the detector. This blockage is called ‘obscuration’. The detector measures the reduction in light intensity and employing a calibration curve, processes the signal to determine particle size.
Now that we know how the system works, let us discuss the basic practices to ensure the accuracy of the fluid analysis. The human factor counts when it comes to the sample preparation to get accurate particle counts. There are several anomalies that must be examined before performing fluid analysis. Improper sample preparation is the number one contributor that impacts the accuracy of the analysis.
Impediments to Proper Sampling
- Contaminated collection vessel – Collecting a sample in a contaminated vessel immediately compromises your accuracy. A typical and easy mistake is initially using a clean sample vessel and then continuing to reuse the same vessel on subsequent samples. It is best to use a separate vessel for each sample for your analysis.
- Improper agitation to suspend the resident particles within the sample – Time and technique will differ depending on the fluid type, contamination type and mass, and length of time sample has been in a static state.
- Little or no degassing is performed to remove the entrained air after proper agitation – Degassing can be performed using an ultrasonic bath, or by vacuum degassing.
- Letting the properly agitated and degassed sample stand for an extended period before sampling – (contributes to particle settling) – The prevailing myth is by letting the sample set for an extended time after sample agitation it allows the sample to degas on its own. At first glance, this thinking is logical until you consider gravity is working steadily to drag those suspended particles (especially the larger or heavier particles) to the bottom of the vessel and thus, causing your sample to appear much cleaner than it is.
- Using a magnetic stirrer with the stir speed set too fast – If a little stirring is good, then a lot is better, right? Unfortunately not, too much speed can create a centrifuge effect and actually drive the particles out of suspension to the inside wall of the vessel, effectively taking them out of the sampling path.
Also, if you see ferrous metals attaching themselves to the stir bar, you must not use it for that sample fluid or it will skew the reported results.
Stir bars can be used (but are not required) to aid in keeping the 50μm (or larger) particles suspended especially while measuring larger sample volumes, however, the stir bar must be essentially particle-free and stirrer speed slow enough to prevent the centrifuge effect and yet fast enough to suspend the contaminants you are attempting to measure.
Importance of Routine Calibration of the Particle Counting System
Particle counters provide the information to determine the health of an industrial fluid system. This is required to evaluate the performance of industrial equipment, verify the cleanliness of hydraulic fluid for service and the quality of fuel produced for commercial purposes. Over 90% of catastrophic failures are the result of abrasive wear that can cause the pumps, valves, precision mechanical components, or other fluid power systems to fail.
The mining and petroleum industries make use of equipment that operate in demanding environmental conditions and are continually exposed to the contamination of dust and dirt, extensive hours of operation and extreme ranges in temperature. 75-80% of hydraulic failures are because of particle contamination.
It is vital and highly recommended by manufacturers as well to regularly calibrate (configure an instrument to provide accurate measurements or information) these systems.
The accuracy of particle counters degrades over time, but regular (at least annual) calibration is the best way of minimizing this degradation and maintaining the accuracy of your system.
For commercial purposes, fluid power-producing companies are required to produce the calibration certification to confirm that the product has been tested and validated for use.
Generally, laboratories are required to comply with ISO standards and must hold accreditation in order to be deemed technically competent. Without the routine calibrations, companies are at a risk of losing their accreditation which will highly impact productivity and profitability.
Related Products:
HIAC PODS+ HIAC 8011+
Sourced from materials provided by our partner - Beckman Coulter
Compiled and Modified by Pheby Mahoney (Marketing and Insights Associate at Cleanearth Scientific Limited)
No comment yet, add your voice below!